Do you know the selection guidelines of SD card socket connector?
- Share
- publisher
- MOARCONN
- Issue Time
- May 17,2025
Summary
Here is the SD card socket connector selection guidelines:
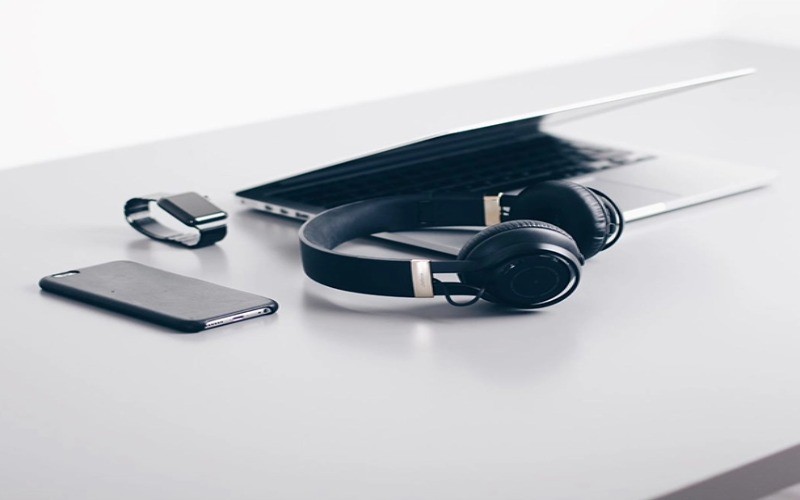
Here is the SD card socket connector selection guidelines:
1. Environmental Adaptability
1. Temperature Range
Industrial environments may face extreme temperatures (e.g., -40°C to +85°C). Select connectors with wide-temperature designs.
- Material Selection: Use high-temperature-resistant materials (e.g., LCP resin or metal-shielded housings) to prevent deformation or performance degradation.
2. Protection Rating
- Dust/Water Resistance: Prioritize IP67 or higher ratings, especially for dusty, humid, or liquid-exposed environments.
- Anti-Corrosion: Opt for stainless steel housings or anti-sulfuration-treated materials in corrosive conditions.
3. Vibration/Shock Resistance
- Use stable locking mechanisms (e.g., spring locks or slide locks) to prevent SD card dislodgment under vibration.
- Select high-elasticity contact materials (e.g., gold-plated phosphor bronze) to maintain pressure over long-term use.
2. Mechanical Structure & Reliability
1. Insertion Cycles
Industrial connectors should withstand ≥5,000 cycles (up to 10,000 for high-end models).
- Self-Ejecting Designs reduce manual wear and extend lifespan.
2. Anti-Misinsertion Features
- Polarized slots (unique shapes) or anti-reverse structures prevent signal errors or hardware damage.
3. Mounting Options
- Surface Mount (SMT) saves PCB space for compact devices; Through-Hole (THT) suits high mechanical stress scenarios.
3. Electrical Performance
1. Contact Resistance & Current Capacity
- Contact resistance <80mΩ; gold-plated terminals minimize oxidation.
- Ensure ≥0.5A current rating (higher for power pins).
2. EMI Shielding
- Metal housings (e.g., stainless steel) with shielding layers suppress electromagnetic interference (EMI).
- Solder cable shielding to connector housing for continuous EMI protection.
3. Voltage/Insulation
- Withstand ≥500V AC; insulation resistance ≥1000MΩ to prevent breakdown or leakage.
4. Supply Chain & Cost Control
1. Supply Stability
- Prioritize domestic suppliers (e.g., MOARCONN) to mitigate international logistics/trade risks.
- Standardized models simplify bulk procurement.
2. Cost Balance
- Balance higher upfront costs of industrial connectors against long-term maintenance savings.
5. Certifications & Standards
1. Compliance
- Meet IEC, UL (e.g., UL94V-0 flame resistance), and automotive standards like TS16949 if applicable.
2. Customization
- Partner with suppliers offering joint development (e.g., PTM mode) for unique size/interface needs.
6. Application-Specific Design
- Consumer Electronics: Lightweight (e.g., 1.1mm height) for portability.
- Industrial Control: Metal housing + high cycle life for vibrating machinery.
- Automotive: Shock/temperature resistance for dashcams or navigation systems.
Summary
Prioritize environmental harshness (temperature, vibration, EMI), insertion cycles, electrical performance, and supply stability. Recommended models include MOARCONN FCD407 (SMT, 5,000 cycles) or MOARCONN 47219 (hinged lock, EMI shielding). For extreme conditions, consider custom solutions (e.g., metal housing + wide-temperature materials). Finalize based on specific robotic applications (e.g., industrial automation or automotive).