SD Card Connector Design and Manufacturing: Insights from Industry Leaders
- Share
- publisher
- MOARCONN
- Issue Time
- Jul 2,2025
Summary
SD Card Connector Design and Manufacturing: Insights from Industry Leaders.
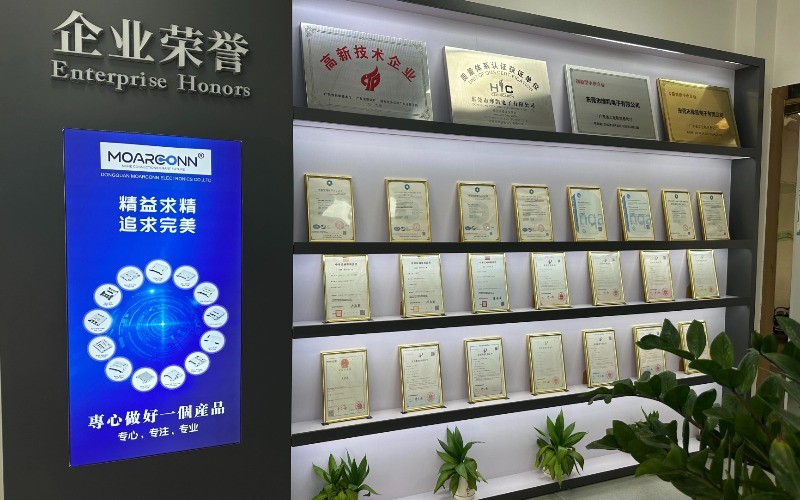
Introduction
In the age of compact and high-speed storage, SD card connectors are indispensable components powering countless electronic devices—from smartphones to industrial control systems. This page offers a deep dive into the structural design, material selection, and manufacturing precision behind modern SD card connectors, drawing on best practices from top industry players.
1. Evolution of SD Card Connector Design
The structural evolution of SD connectors reflects increasing demands for miniaturization, durability, and signal integrity. According to WIN SOURCE, key trends include:
Reduced connector height and footprint for tighter PCB layouts
Push-push and push-pull mechanisms to optimize insertion/removal cycles
Card detection switch designs for reliable status feedback
These features support compact consumer electronics, medical devices, and even embedded Linux systems as detailed in Acme Systems.
2. Key Design Considerations
High-performance SD card connectors must address several critical engineering concerns:
✅ Contact reliability under frequent insertions (≥10,000 cycles)
✅ Material choices like LCP (liquid crystal polymer) for heat resistance during SMT reflow
✅ EMI shielding for data integrity in high-frequency environments
✅ Switch pin mechanisms to enable hot-swap detection
3. Precision Manufacturing in SD Card Connectors
Modern SD card connector manufacturing involves a combination of:
High-precision stamping for contact terminals
LCP injection molding for housing structure
Automatic assembly & visual inspection systems to ensure consistency
100% functional testing including insertion force, resistance, and signal integrity
As noted by Full Glory Electronics, a connector's durability is only as good as its manufacturing precision.
4. Application-Specific Customization: A Competitive Advantage
At Moarconn , we understand that no two customers have identical needs. That's why we offer tailor-made SD card connector solutions including:
Customized pin counts and switching mechanisms
Application-driven height/angle optimization (especially for mobile and IoT devices)
Industrial-grade designs for high-vibration environments
With over 10+ years of connector R&D and manufacturing expertise, Moarconn connectors meet global standards (ISO, CE, RoHS) and are widely used across telecom, automotive, and embedded computing industries.
🔗 Learn more at www.moarconn.com
5. What Sets Industry Leaders Apart
Through extensive benchmarking of market leaders, a few characteristics stand out:
Feature
Insertion Durability
LCP Housing Quality
Custom OEM/ODM Options
Lead Time
ndustry Standard
5,000+ cycles
Grade B or above
Limited
6–8 weeks
Moarconn Advantage
10,000+ cycles
Grade A LCP for heat tolerance
Full project-level customization
As fast as 3–4 weeks
Conclusion: Building the Future of Embedded Storage
SD card connectors are more than just mechanical interfaces—they’re vital to the functionality, speed, and reliability of storage in modern electronics.
By collaborating with forward-looking suppliers like Moarconn, engineers can ensure they select connectors that are not only durable and efficient—but engineered for tomorrow’s challenges.
📩 Contact us to request free samples or download technical drawings for your next project.